Quality Assurance
Consistently Delivering High-Quality Parts.
Quality Is Our No.1 Priority
for All CNC Precision Machining Parts
Manufacturers choose CNC machining because it offers several advantages. Although CNC machining can ensure higher productivity and fewer errors than traditional machining, quality inspection is still an indispensable part of the manufacturing process.At Kachi machining,our committed to an operating philosophy that exceeds our customer’s expectations for quality, safety, cost, delivery and value. In order to meet customer expectations, trade standards and industry regulations,Kachi machining uses different measuring instruments and tools to control the quality of CNC machining parts.
CMM Inspection
What is CMM inspection?
CMM inspection delivers the precise dimensional measurements of an object component by scanning a huge number of X, Y, Z coordinates of its surface. There are various CMM methods to record the geometric dimensions, with touch-probes, light, and lasers being the most common. All measured points result in the so-called point cloud. That data can be compared to an existing CAD model to determine the dimensional deviation.
Why CMM inspection is important?
In many areas, the exact dimensions are decisive for the quality of products. For components such as housings, threads, and brackets, the dimensions must remain within tight tolerance limits.
In motors and gearboxes, even the slightest deviation in measurement - such as a thousandth of a millimeter - can have negative effects on the performance of the parts and the machine as a whole.
With the latest 3D Coordinate Measuring Machine (CMM) technology, Kachi CMM inspection services allow the precise measurement of components as part of quality assurance.
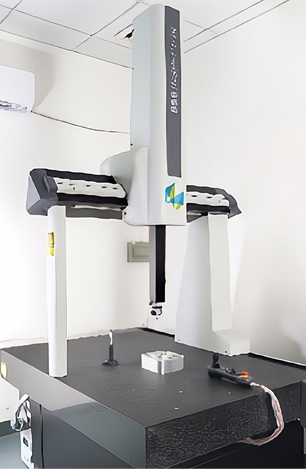
CMM
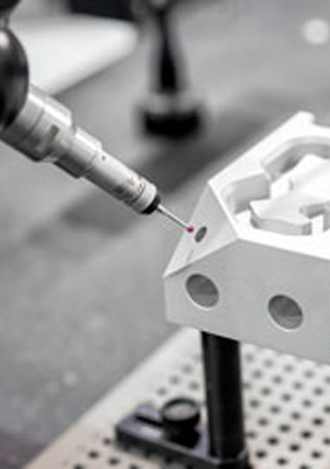
CMM Part Fixturing
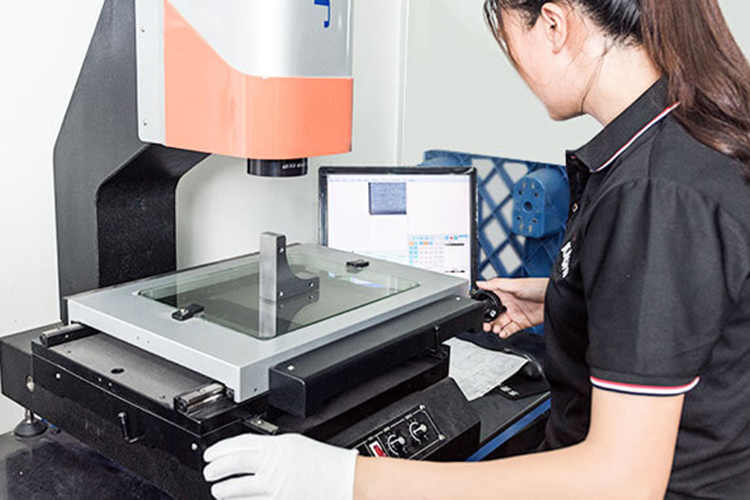
Profile Projector
Profile projectors are used to measure the profile and dimensions of machined parts. They can be used to check the dimensions of complex parts, such as gears, to ensure they meet the required specifications.
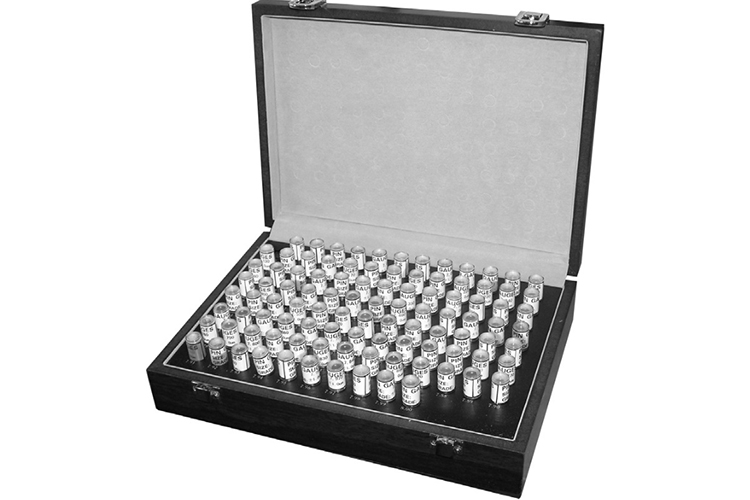
PIN Gauges
Precision measuring tools used to measure the diameter of holes. They consist of a set of cylindrical rods with precisely defined diameters. PIN gauges are used to measure the diameter of holes during the manufacturing process.
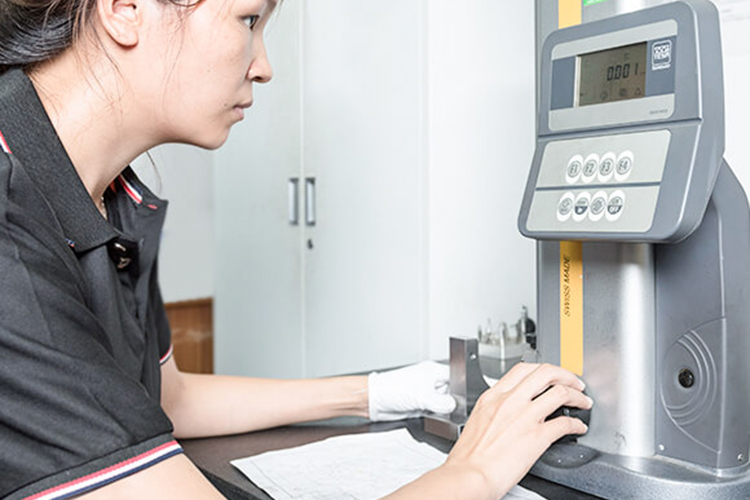
Height gauge
Height gauge is a tool for measuring the height of the parts. It’s also a useful way to mark the surface of the objects and parts. For example, when we need to process the parts with a specific size, we can use a height gauge to leave marks on them.
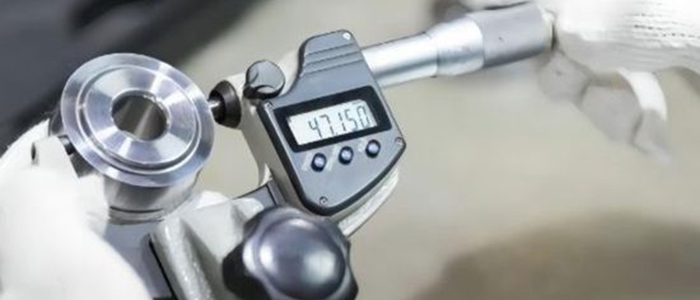
Vernier Caliper
Vernier caliper is an easy-to-use tool, which measures the parts in linear dimensions. We can get the measurement by using the final markings on a linear dimension.
It is often applied to measure the diameters of round and cylindrical parts. For the engineers, it is convenient to take and check the small parts.
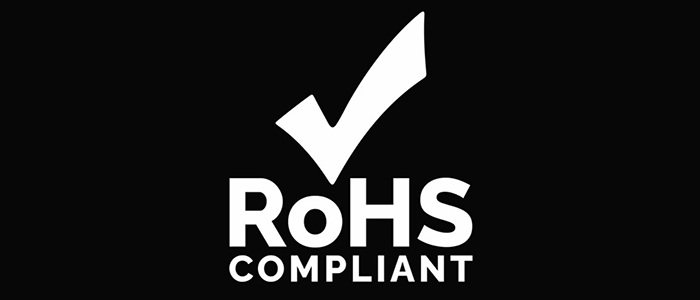
Material Certifications
We can provide a RoHS report according to the customer’s request that verifies the compliance of a specific material or product with the RoHS directive.
Kachi Manufacturing Standards
of CNC Machining Services
For features of size (length, width, height, diameter) and location (position, concentricity, symmetry) +/- 0.005” (metals) or +/- 0.010 (plastics and composites) by ISO 2768 unless otherwise specified.
Sharp edges will be broken and deburred by default. Critical edges that must be left sharp should be noted and specified on a print.
As machined surface finish is 125 Ra or better. Machine tool marks may leave a swirl-like pattern.
Clear or transparent plastics will be matte or have translucent swirl marks on any machined face. Bead blasting will leave a frosted finish on clear plastics.
For features of orientation (parallelism and perpendicularity) and form (cylindrical, flatness, circularity, and straightness) apply tolerances as follows (see the table below):
Limits For Nominal Size | Plastics (ISO 2768- m) | Metals (ISO 2768- f) |
0.5mm* to 3mm | ±0.1mm | ±0.05mm |
Over 3mm to 6mm | ±0.1mm | ±0.05mm |
Over 6mm to 30mm | ±0.2mm | ±0.1mm |
Over 30mm to 120mm | ±0.3mm | ±0.15mm |
Over 120mm to 400mm | ±0.5mm | ±0.2mm |
Over 400mm to 1000mm | ±0.8mm | ±0.3mm |
Over 1000mm to 2000mm | ±1.2mm | ±0.5mm |
Over 2000mm to 4000mm | ±2mm | |
All parts are deburred. Tightest achievable tolerance is +/-0.01mm and is dependent on part geometry. |
Manufacturing Standards
of Sheet Metal Fabrication Services
Kachi Machining has the experience and the right sheet metal fabrication services necessary to bring your idea to life.
This includes services like high tolerance and wide thickness range laser cutting, bending capabilities, and other Surface finishing options.
Has the experience and the right sheet metal fabrication services necessary to bring your idea to life.
Dimension Detail | Tolerance |
Edge to edge, single surface | +/-0.005 inch |
Edge to hole, single surface | +/-0.005 inch |
Hole to hole, single surface | +/-0.010 inch |
Bend to edge / hole, single surface | +/-0.030 inch |
Edge to feature, multiple surface | +/-0.030 inch |
Over formed part, multiple surface | +/-0.030 inch |
Bend angle | +/-1° |
By default, sharp edges will be broken and deburred. For any critical edges that must be left sharp, please note and specify in your drawing. |
Inspection Equipment
Item | Equipment | Working Range |
1 | CMM | X-axis: 2000mm Y-axis: 2500m Z-axis: 1000mm |
2 | Profile Projector | 300*250*150 |
3 | Height Gauge | 700 |
4 | Digital Callipers | 0-150mm |
5 | 0-150mm | 0-50mm |
6 | Thread Ring Gauges | Various Thread Types |
7 | Thread Ring Gauges | Various Thread Types |
8 | PIN Gauges | 0.30- 10.00mm |
9 | Block Gauges | 0.05 - 100mm |