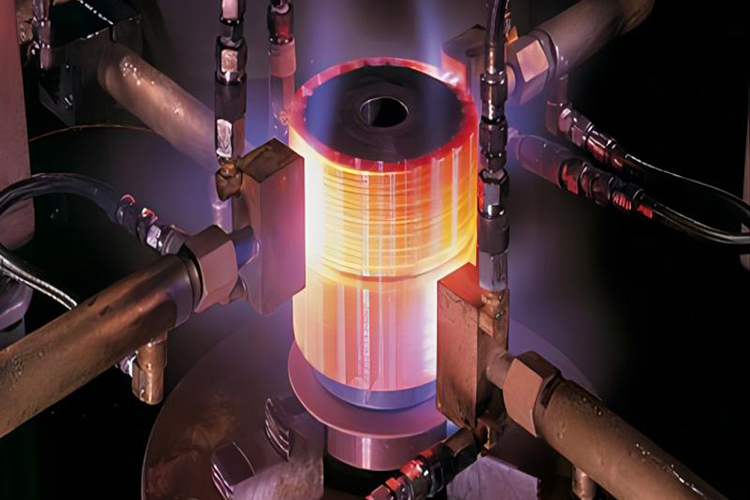
Heat Treating
Heat treatment is an essential step in precision machining. However, there is more than one way to accomplish it, and your choice of heat treatment depends on materials, industry and final application.
Heat Treating Services
Heat treating metalHeat treating is the process by which a metal is heated or cooled in a tightly controlled environment to manipulate physical properties such as its malleability, durability, fabricability, hardness, and strength. Heat-treated metals are imperative to many industries including the aerospace, automotive, computer, and heavy equipment industries. Heat treating metal parts (such as screws or engine brackets) creates value by improving their versatility and applicability.
Heat treatment is a three-step process. First, the metal is heated to the specific temperature needed to bring about the desired change. Next, the temperature is maintained until the metal has been evenly heated. The heat source is then removed, allowing the metal to cool completely.
Steel is the most common heat treated metal but this process is performed on other materials:
● Aluminum
● Brass
● Bronze
● Cast Iron
● Copper
● Hastelloy
● Inconel
● Nickel
● Plastic
● Stainless Steel
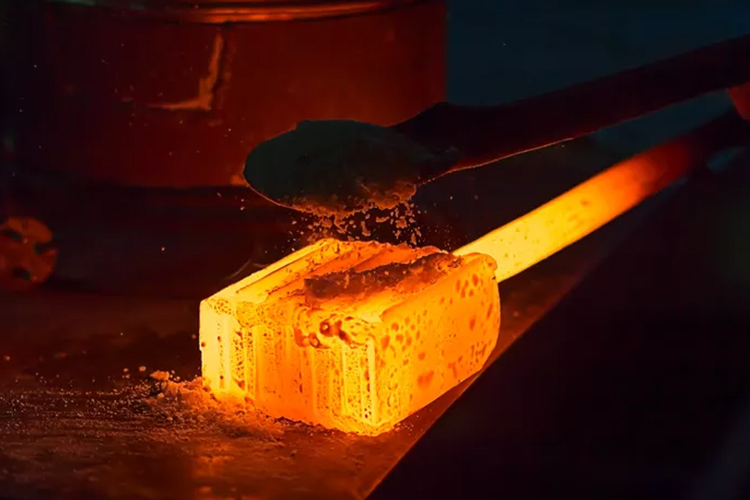