Custom Sheet Metal
Fabrication Services
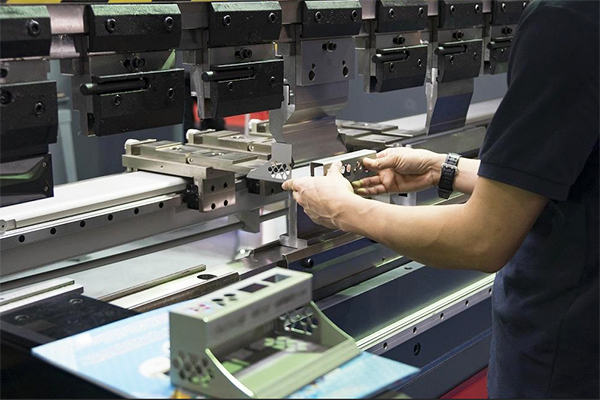
Sheet Metal Processing
The sheet metal processing technology is complex and diverse, mainly including cutting, blanking, bending, etc. At the same time, it also provides services such as laser cutting, spraying screen printing, and assembly according to the customer's drawing design requirements.
Let's begin by looking at what sheet metal fabrication entails before moving on to the individual steps that result in metal parts and products.
CNC Machined Metal Prototypes
The traditional way to make metal prototypes is through CNC machining. We would utilize a combination of a milling machine and lathe to create your prototype.
This option takes a little longer than 3D printing or using sheet metal, but you’re left with a strong part. Also, CNC machines can handle a wide range of material options and thicknesses, so you have plenty of freedom when it comes to designing.
We can apply finishing steps to a CNC machined part, changing the color and surface characteristics.
CNC machining might be more expensive, depending on your specific product. It’s still a great option for low-batch production runs, and you can use the same CNC machining operation to make medium-scale production runs.
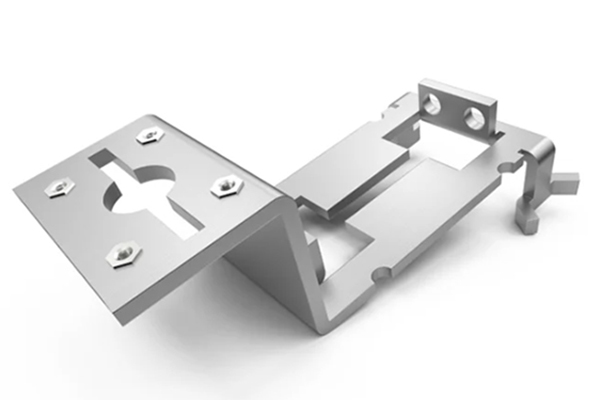

Engineering Materials For Sheet Metal Prototype Fabrication
Creating a prototype of your product can help you to select the right metal material for your product, tweak dimensions, and improve functionality. Ultimately, this makes the final production run more cost and time efficient.
Various metals are used to create sheet metal prototypes depending on the application and roles. Manufacturers use different grade metals for prototyping sheet metal products. Some metal options that can be used for metal prototypes are:
Aluminum | copper | Steel |
Aluminum 1050 | Copper 1020 | Stainless Steel 301 |
Aluminum 5052 | Copper 1100 | Stainless Steel 303 |
Aluminum 6061 | Copper 2100 | Stainless Steel 304 |
Aluminum 6063 | Copper 2200 | Stainless Steel 430 |
Aluminum 1100 | Copper 2300 | Stainless Steel 316/316L |
Copper 2400 | Steel,Low Carbon | |
Copper 260(Brass) |
How Does Sheet Metal Fabrication Work
Depending on the type of part to be manufactured, the complexity of the design and the desired finish, metal sheets may be formed in 3 simple steps namely cutting, forming, and joining. (assembly)
- Cutting
Cutting operations in sheet metal processing may be done with/without shear. - The shear cutting processes
Are blanking, cutting, and shearing. Non-shear processes are more precise and tailored for high-accuracy industrial end products. - Non-shear processes
Include laser beam cutting, water jet cutting, plasma cutting, and machining. They are more suitable for industrial use in automotive and aerospace, robotics, and sometimes engineering. - Laser cutting:
Applies a laser-focused light beam to cut through metal sheets. It can also be used for engraving sheet metals.
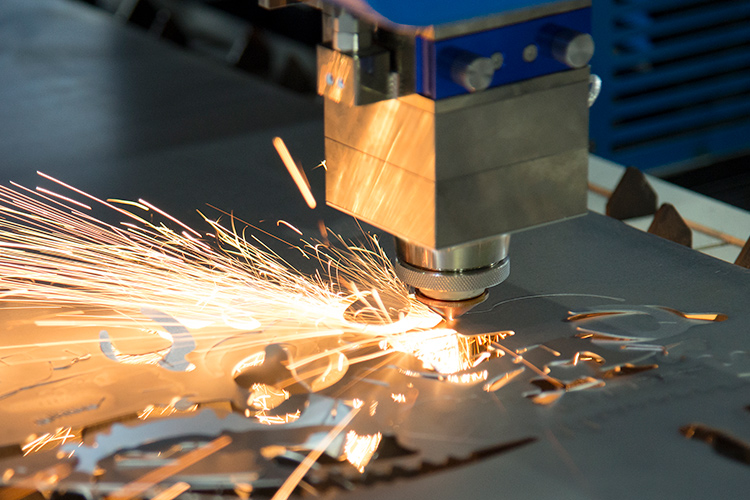
- Water jet cutting:
A high-velocity process that directs abrasive-concentrated streams of water at the sheet to cut into the material. - Machining:
Can be conventional or CNC-based. This process involves the use of a tool (drill bits or lathe blades) to systemically remove pieces of material from a part. CNC milling, spinning, and turning are some of the most popular processes. - Plasma:
Plasma cutting uses heat-compressed ionized gases that travel at high speed and conduct electricity to direct cuts at a metal sheet. - Forming:
Forming is the general umbrella for processes like stamping, stretching, roll-forming, and bending. Unlike cutting where the material is removed from sheet metal, forming simply uses fabrication tools to reshape the part to the desired geometry. - Stamping:
A forming technique involves the use of two dies to press the metal into the desired shape. - Bending:
Contours a sheet metal, and can be done by hand or brake press, while roll-forming uses a pair of rolls to process an entire length of sheet metal into a coil. - Joining:
Joining is usually but not necessarily the final process in sheet metal fabrication. It involves processes like riveting, adhesives, brazing, and most popularly, welding. - Welding:
May be Stick, MIG, or TIG. The process essentially fuses two or more metal sheets by using a flame to melt them together in the presence of a filler. - Riveting
Joins sheet metals together by embedding small metal parts through both sheets. - Adhesives:
High-end glues that are capable of holding sheet metals together on their own or when used in conjunction with any other joining process. - Brazing:
Brazing is similar to welding, with the only difference being that the metal sheets are not melted, only the filler.
Once the metal part has been fabricated and assembled, a host of finishing processes (detailed below) can be used to improve its properties and appearance.
Request A Quote
Ready to Start Your Custom Sheet Metal Fabrication Project with Kachi?
Click here to get in touch with us and get a free quote now!